18.07.25 – Modernisierung
Thyssenkrupp Steel investiert gewaltig am Kernstandort Duisburg
Deutschlands größter Stahlhersteller hat am Standort Duisburg die Stranggießanlage 4 und das Warmbandwerk 4 modernisiert und optimiert.
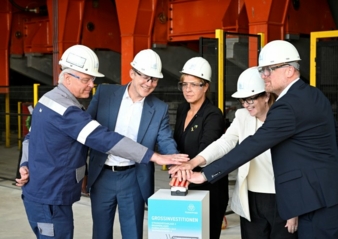
Von links: Dr. Harald Espenhahn, Head of Technology, Environment & Maintenance, Dennis Grimm, Vorstandsprecher von Thyssenkrupp Steel, Mona Neubaur, Wirtschafts- und Klimaschutzministerin NRW, Ise Henne, Aufsichtsratssvorsitzende Thyssenkrupp Steel, und Sören Link, Oberbürgermeister der Stadt Duisburg, geben der neuen Anlage das GO. © Thyssenkrupp Steel Europe
Nach rund zwei Jahren Bau- und Montagezeit: Mit den nun fertiggestellten Kernaggregaten hat Deutschlands größter Stahlhersteller sein Produktionsnetzwerk an entscheidenden Schnittstellen modernisiert und optimiert. Im Zentrum des Großprojekts standen die neue Stranggießanlage 4, das umfassend modernisierte Warmbandwerk 4 mit zwei neuen Hubbalkenöfen und eine vollautomatisierte Brammenlogistik. Damit verfügt Thyssenkrupp Steel nach eigenen Angaben nun über einen der modernsten Anlagenverbünde der europäischen Stahlindustrie. Die Aggregate ersetzen die über 20 Jahre alte Gießwalzanlage, um die steigenden Kundenanforderungen und höchsten Materialanforderungen auch zukünftig optimal bedienen zu können. Mit rund 800 Mio. Euro ist dieses Investitionsprojekt eines der größten in der Geschichte des Unternehmens.
Dennis Grimm, Vorstandssprecher von Thyssenkrupp Steel, betont: „Dieses Projekt ist ein entscheidender Meilenstein, um unsere Technologie- und Qualitätsführerschaft zu stärken und den steigenden Anforderungen unserer Kunden gerecht zu werden. Trotz eines sehr herausfordernden wirtschaftlichen Umfelds können wir rund 800 Millionen Euro investieren, um damit unsere Position im Wettbewerb weiter zu verbessern. Das ist ein starkes Signal für den Stahl und den Standort Duisburg. Hier entsteht Zukunft.“ Wirtschafts- und Klimaschutzministerin Mona Neubaur: „Mit der neuen Anlagentechnik in Duisburg wird ein wichtiger Schritt zur Modernisierung der Stahlproduktion in Nordrhein-Westfalen umgesetzt. Die Investition zeigt unternehmerische Verantwortung für den Standort und trägt zur Steigerung von Qualität, Effizienz und Flexibilität bei. Sie stärkt die industrielle Wertschöpfung in Bereichen wie Fahrzeugbau und Energieversorgung. Damit bleibt NRW ein wettbewerbsfähiger Industriestandort.“
Stabile Prozesse
Die neuen Aggregate befinden sich an der Schnittstelle zwischen Flüssigphase und Warmbanderzeugung und sind damit ein Kernstück des integrierten Produktionsverbundes im Duisburger Norden. Durch die jetzt abgeschlossene Neukonfigurierung kann neben den Qualitätssteigerungen durch eine Erhöhung der Gieß- und Walzkapazitäten auch eine bessere Auslastung des vorgeschalteten Oxygenstahlwerks 1 erzielt werden. Damit wird die Gesamtperformance des Produktionsnetzwerks noch einmal an einer zentralen Stelle gesteigert - mit nachhaltig positiven Auswirkungen auch auf die Versorgungsicherheit der Kunden.
Die neue Stranggießanlage 4 ersetzt den Gießteil der alten Gießwalzanlage und sorgt für eine hochpräzise, flexible und effiziente Brammenproduktion. Die Anlage zeichnet sich darüber hinaus durch bessere Reinheitsgrade, eine verbesserte Formgenauigkeit und Oberflächenqualität aus.
Das dahinter geschaltete, auf rund 3 Mio. Tonnen ausgelegte und umfassend modernisierte Warmbandwerk 4 wurde mit zwei neuen Hubbalkenöfen ausgestattet, die für eine präzisere Walzgenauigkeit und vor allem für eine optimierte Oberflächenqualität sorgen. Modernste Steuerungssysteme gewährleisten engste Dickentoleranzen, optimierte Abkühlprozesse verbessern nochmals die Materialeigenschaften des Warmbands. Die in Naturkante eingesetzten Brammen können zudem in deutlich flexibleren Abmessungen produziert werden und erlauben in Summe ein erweitertes Produktspektrum, zum Beispiel hinsichtlich hochfester Güten sowie bei Dynamo- und Trafostählen.
Bindeglied Bramme
Die komplett neu erstellte Brammenlogistik ist das Bindeglied zwischen beiden Aggregaten. Sie sorgt für eine vollautomatisierte, weitgehend digitale Prozessabwicklung. Modernste Steuerungssysteme erlauben die Echtzeit-Synchronisation von rund 1,7 Mio. t pro Jahr. Damit wird ein maximal flexibler und effizienter Prozessfluss im neuen Anlagenverbund erreicht.
Alle neuen Anlagen zeichnen sich durch hohe Automatisierungsgrade und modernste Steuerungssysteme aus, indem zum Beispiel durch den Einsatz digitaler Twins eine Echtzeitüberwachung der Produktionspresse ermöglicht wird. Auch dies dient einer konsistenten und durchgehend optimierten Produktqualität.
Eckdaten
Warmbandwerk 4
- Länge: 360 m
- Nenn-Kapazität p. a.: 3,1 Mio t
- Bandbreiten: 900 mm bis 1600 mm
- Banddicken: 1,2 mm bis 9,0 mm
Hubbalkenöfen 1 und 2
- Temperaturbereich: bis zu 1300 °C
- Länge: ca. 62 m
- Breite: ca. 11 m
- Max. Leistung pro Ofen: 380 t/h bei Kalt- und 560 t/h bei Direkteinsatz
- Max. Brammenlänge: 10 m
- Max. Geschwindigkeit: 25 m/h
- Mischgasbefeuerung
Stranggießanlage 4
- Metallurgische Länge: 35,5 m
- Norm-Kapazität p. a.: 2,3 Mio. t
- Brammenbreite: 900-1800 mm
- Brammendi >Vollautomatisiert mit intelligenter Logistiksteuerung
- Echtzeit-Synchronisation von ca. 1,7 Mio. Tonnen Brammen/Jahr
- Deutlich erhöhte Betriebssicherheit, minimaler Personaleinsatz