30.11.23 – Exzellenz-Preis von WZL Aachen und Fraunhofer IPT
Beim Umformwerkzeugbau ist die markante BMW-Nase ganz vorn
Es war ein schwieriges Jahr, betonte die Jury des Wettbewerbs »Excellence in Production«, die in diesem Jahr bereits zum 20. Mal die Werkzeugbauteams des Jahres kürte. Digitalisierung, Vernetzung, strategische Ausrichtung, komplexes Konstruktions-Verständnis, Praktikabilität und BWL-Knowhow zeigten alle Sieger-Teams, darunter viele Mittelständler, auf.
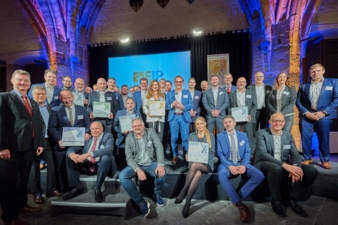
Gruppenbild mit Damen: der Exzellenz-Preis im Umformwerkzeugbau hat die besten aus Mittelstand und Industrie, Jung und Alt, Frauen wie Männer angezogen. Der Wettbewerb findet alljährlich im deutschsprachigen Raum statt und wird vom WZL Aachen und dem Fraunhofer IPT zusammen mit Unternehmens-Sponsoren gestemmt. © Fraunhofer IPT
Die starke Konkurrenz aus dem asiatischen Raum und ein enormer Preisdruck bei gleichzeitig hohen Kundenanforderungen machten allen Betrieben zu schaffen, vor allem jedoch den externen Werkzeugbaubetrieben. Umso herausragender sei die Leistung der Unternehmen zu benennen, die dieses Jahr im Finale standen. Die internen Werkzeugbaubetriebe zeigten im Teilnehmerfeld der Finalisten gleichermaßen starke Leistungen und stellten schließlich auch den Gesamtsieger, den BMW-Umformwerkzeugbau der Werke München und Dingolfing.
Der Münchner und Dingolfinger Werkzeugbau setzte sich damit in einem Teilnehmerfeld von insgesamt 305 Unternehmen durch, aus denen in vier Kategorien insgesamt zwölf Finalisten hervorgingen. Am 15. November nahm das Team der BMW-Umformer während einer feierlichen Preisverleihung im Aachener Rathaus vor rund 300 Gästen den begehrten Preis entgegen. Die Laudatio auf den Gesamtsieger hielt traditionsgemäß der Vorjahressieger – in diesem Jahr Michael Stepper, Inhaber und Geschäftsführer der Fritz Stepper GmbH & Co. KG.
Augmented-Reality-Anwendungen
Ausschlaggebend für die Jury waren besonders die starke strategische Positionierung des Werkzeugbaus als Design-Enabler innerhalb des Konzerns und der stringente Einsatz von Industrie-4.0-Technologie und Digitalisierung. Herausragendes Beispiel dafür ist die konsequente Nutzung von Augmented Reality in der Qualitätsprüfung und zur Digitalisierung des Fachwissens der Mitarbeitenden. Der Umform-Werkzeugbau ist Teil des weiten Produktionsnetzwerks der BMW Group und beschäftigt 480 Mitarbeitende, davon 68 Auszubildende. Der Münchner und Dingolfinger BMW-Werkzeugbau legt einen starken technologischen Fokus auf seine Kernkompetenz des Fräsens und verfügt in dieser Technologie über einen hohen Automatisierungsgrad. Mit seiner technologischen Ausstattung und dem dazugehörigen Know-how ist der Werkzeugbau außerordentlich gut in die vor- und nachgelagerten Kundenprozesse integriert und stellt darüber hinaus ein breites Dienstleistungsangebot bereit, zu dem auch datenbasierte Dienstleistungen zählen, beispielsweise die Sensor-Überwachung des Werkzeugs beim Kunden.
Mit seiner Expertise für die Außenhaut sichert er auf globaler Ebene den Anlauf für die Fahrzeugprojekte des Konzerns. Seine Prozesse orientieren sich am Prinzip »Lean. Green. Digital« der BMW-iFactory-Strategie, die eine effiziente, präzise und hochflexible Produktion mit dem Nachhaltigkeitsgedanken und hoher Datentransparenz vereint.
Bereits früh in der Produktentstehung gestalten die Werkzeugbau-Expertinnen und -Experten gemeinsam mit den Designabteilungen das unverkennbare Design der Fahrzeuge. Ob sich die Bauteile wie gewünscht herstellen lassen und die Presswerke in der Lage sind, sie in den geforderten Stückzahlen in höchster Qualität zu produzieren, zeigen exakte Bauteil- und Prozesssimulationen bereits im Vorfeld der Produktion. Hochqualifizierte Mitarbeitende bilden im Unternehmen die Basis für den Erfolg in der Werkzeugherstellung und dem Einsatz beim Kunden. Von der Produktentstehung bis zu Produktionsende, aber auch bei Änderungen oder im Havariefall ist es der Anspruch des internen Werkzeugbaus, seinen Kunden kompetent zur Seite zu stehen.
Bester Werkzeugbau mit mehr als 50 Mitarbeitern
Zusätzlich zum Gesamtsieg erklärte die Jury des Wettbewerbs den internen Werkzeugbau der BMW AG in den Werken München und Dingolfing auch zum Sieger der Kategorie »Interner Werkzeugbau ab 50 Mitarbeitende«. Als weitere Finalisten dieser Kategorie zeichnete die Jury den BMW-Werkzeugbau am Standort Landshut und die Gealan Fenster Systeme GmbH aus Oberkotzau in Oberfranken mit einer Urkunde aus.
Bester Werkzeugbau unter 50 Mitarbeitern
Der Sieg in der Kategorie »Interner Werkzeugbau unter 50 Mitarbeitende« geht in diesem Jahr an die Technoform Insulation Solutions Tooling GmbH aus Kassel. Besonders überzeugte Technoform die Jury durch seine hohe Prozesskompetenz in der Drahterosion. Dafür nutzt das Unternehmen 4-Achs-Bearbeitung sowie selbst hergestellte Aufspannungen zur Reduktion von Rüstaufwänden. Zwei redundante Hallen für Serien und Musterwerkzeuge bilden laut dem Urteil der Jury eine schlüssige Segmentierung des Werkzeugbaus. Einen ausgezeichneten Eindruck hinterließ bei der Jury auch die starke Mitarbeitendenorientierung in Form flacher Hierarchien, hoher Eigenverantwortung der Mitarbeitenden und flexibler Arbeitszeitgestaltung.
Technoform ist ein deutsches, international tätiges Familienunternehmen und spezialisiert auf die Extrusion thermoplastischer Kunststoffprofile für thermische Trennungen in Fensterprofilen und Isolierprofilen. Es beschäftigt an mehr als 45 Vertriebs- und Produktionsstandorten weltweit rund 1600 Mitarbeiterinnen und Mitarbeiter. Der interne Werkzeugbau fertigt jährlich mehrere hundert Muster- und Serienwerkzeuge für den Eigenbedarf. Insgesamt besteht das Team des Werkzeugbaus aus 47 Mitarbeitenden, davon zurzeit sechs Auszubildende.
Als weitere Teilnehmer standen in diesem Jahr die Roto Frank Austria GmbH aus Kalsdorf in Österreich sowie die Schunk Sintermetalltechnik GmbH aus Heuchelheim im Lahn-Dill-Kreis im Finale.
Bester externer Werkzeugbau ab 50 Mitarbeitern
Bester »Externer Werkzeugbau ab 50 Mitarbeitende« im Jahr 2023 wurde die Giebeler GmbH aus Eschenburg bei Gießen.
Bei Giebeler zeigte sich die Jury beeindruckt von der organisatorischen Exzellenz des Unternehmens: Diese äußert sich besonders in der effizienten Kalkulation anhand einer eigens entwickelten App mit geometrischer Ähnlichkeitsanalyse. Die App versetzt das Unternehmen in die Lage, ähnliche Werkzeuge zu identifizieren und die Aufwände schon im Vorfeld der Herstellung auf Basis von Nachkalkulationen zu bestimmen. Hinzu kommt ein hoher Anteil an fertiggestellten Aufträgen ohne Budget- oder Fristüberschreitung – trotz häufiger später Änderungen durch den Kunden. Besonders hebt sich Giebeler auch durch das Vorantreiben des Pay-per-Use Geschäftsmodells hervor. Was bei einigen Maschinen im Maschinenpark bereits zum Einsatz kommt, wird auch schon bei ersten Werkzeugen getestet. Für die Umsetzung des neuen Geschäftsmodells arbeitet Giebeler eng mit Banken und Start-ups im Bereich der Blockchain-Technologie zusammen.
Die Giebeler GmbH beschäftigt insgesamt 180 Mitarbeitende in den Bereichen Werkzeugbau und Kunststofftechnik. Das Familienunternehmen kann auf etwa 11000 hergestellte Werkzeuge zurückblicken. Moderne Technologien, digitale Prozesse und die strategisch nachhaltige Ausrichtung des Werkzeugbaus bestimmen die Entwicklung kundenindividueller Lösungen vom Design bis zur Herstellung von Werkzeugen mit einem Gewicht von bis zu 15 Tonnen. Zur Erprobung der Werkzeuge stehen Spritzgießmaschinen mit bis zu 16000 kn Zuhaltekraft bereit. Der unternehmensinterne 24-Stunden-Werkzeugservice steht Kunden von Giebeler bei Bedarf schnell zur Seite. Das Unternehmen nutzt zudem eigene Datenbanksysteme wie die »Giebeler App« und die »Giebeler Sphere«, um jederzeit Zugriff auf aktuelle Projektdaten zu erhalten. Weitere Finalisten in dieser Kategorie waren die Fischer GmbH aus dem sächsischen Geringswalde sowie die weba Werkzeugbau Betriebs GmbH mit ihren Standorten in Dietach in Österreich und Olomouc in Tschechien.
Bester externer Werkzeugbau unter 50 Mitarbeitern
Gewinner in der Kategorie »Externer Werkzeugbau unter 50 Mitarbeitende« ist die Primaform AG aus Thun in der Schweiz. Besonders positiv bewertete die Jury bei Primaform die gezielten Investitionen in neue Technologien wie die Laserstrukturierung und das Nass-Fräsen von Graphitelektroden. Zudem verfüge der Werkzeugbau über ein sehr gutes Montagekonzept nach dem Prinzip der Fließfertigung mit aufgabenbezogenen Arbeitsplätzen, höhenverstellbaren Tischen und Viewern an jedem Arbeitsplatz. Durch hohe Prozesskompetenzen im Fräsen und Erodieren mit hohem Automationsgrad erreicht Primaform sehr hohe Präzisionsbereiche.
Die Primaform AG mit Sitz in Thun der Schweiz beschäftigt 43 Mitarbeitende und neun Auszubildende. Komplexe Ein-, Mehrkomponenten- und Hybridwerkzeuge für den Spritzguss in der Medizintechnik- und Healthcare-Branche sind heute Kerngeschäft des Unternehmens. 50 bis 60 Werkzeuge mit bis zu 96 Kavitäten, einem Maximalgewicht von fünf Tonnen und Seitenlängen von einem Meter verlassen jedes Jahr das Werk in Thun. Der hochautomatisierte Maschinenpark umfasst neben den klassischen Fertigungstechnologien des Werkzeugbaus auch spezielle Prozesse wie das Texturieren von Oberflächen und die Herstellung kleinster Strukturen mit dem Laser. Außerdem stellt Primaform AG Spritzgießwerkzeuge mit elektrischen Antrieben und eigener Steuerungssoftware her. Das Leistungsangebot umfasst die gesamte Prozesskette, von der kunststoffgerechten Teilekonstruktion über die Prozessentwicklung bis zur Qualifizierung der Produkte und Betriebsmittel.
Als weitere Finalisten in der Kategorie »Externer Werkzeugbau unter 50 Mitarbeitende« wurden die BBG GmbH & Co. KG aus dem Unterallgäu und die Klaucke & Meigies Formenbau GmbH aus Lüdenscheid im Sauerland ausgezeichnet.
Zusätzliche Preise in Sonderkategorien
Anlässlich des Wettbewerbsjubiläums vergaben die Veranstalter in diesem Jahr erstmals Preise in den beiden Sonderkategorien »Beste Nachhaltigkeitsinitiative« und »EiP-Newcomer des Jahres« zur Auszeichnung des besten Erstteilnehmers. Mit dem Preis »Beste Nachhaltigkeitsinitiative« wurde der BMW Werkzeugbau am Standort Landshut ausgezeichnet. Die Jury sieht ihn als Pionier der Kreislaufwirtschaft, der bereits heute hohe Re-Use-Quoten von Werkzeugkomponenten aufweist. Auffällig ist die hohe Präsenz des Themas Nachhaltigkeit auf dem Shopfloor, beispielsweise durch beschriftete Trennbehälter oder das teilweise Energiemonitoring von Maschinen und Anlagen. Besonders lobte die Jury die soziale Komponente der Nachhaltigkeit, die in Form ansprechender Sozial-Räume, sehr guter Ergonomie an allen Arbeitsplätzen und eines umfangreichen Gesundheitsprogramms für die Mitarbeitenden sowie hoher Inklusionsquote gelebt wird.
Der zweite Sonderpreis zum »EiP-Newcomer des Jahres« ging an den internen Werkzeugbau der VOSS Automotive GmbH, die VOSS Werkzeugtechnik GmbH. VOSS überzeugte die Jury durch gezielte Investitionen in Maschinen mit hoher Leistungsfähigkeit und hohem Automatisierungsgrad sowie den Aufbau einer neuen, komplett klimatisierten Fertigungshalle. Beim Besuch vor Ort glänzte VOSS Werkzeugtechnik durch einen hohen Standard an Ordnung und Sauberkeit in der Lagerhaltung sowie auf dem gesamten Shopfloor durch konsequente Anwendung der 5S-Methode.
Info "Excellence in Production"
Das Werkzeugmaschinenlabor WZL der RWTH Aachen und das Fraunhofer-Institut für Produktionstechnologie IPT ermittelten auch in diesem Jahr gemeinsam mit einer fachkundigen Jury die besten Werkzeug- und Formenbaubetriebe im deutschsprachigen Raum in vier Kategorien. Grundlage des ausführlichen Vergleichs bildeten ein umfangreicher Fragebogen sowie Vor-Ort-Besuche der bestplatzierten Unternehmen während der Sommermonate. Auf dieser Basis bestimmten die zehn Juroren aus Industrie, Politik, Verbänden und Wissenschaft zwölf Finalisten, die Kategoriesieger sowie den Gesamtsieger. Insgesamt hatten sich im Jahr 2023 305 Werkzeug- und Formenbaubetriebe am Wettbewerb beteiligt, 217 von ihnen hatten den Fragebogen vollständig ausgefüllt, 50 kamen in die engere Auswahl.
Der Wettbewerb »Excellence in Production« feierte in diesem Jahr bereits sein 20. Jubiläum. Am Tag nach der Preisverleihung stellten ausgewählte Finalisten und Partner der Aachener Institute ihre Erfolgsstrategien während des mittlerweile bereits 22. Internationalen Kolloquiums »Werkzeugbau mit Zukunft« vor. Unter dem Motto »Werkzeugbau – Innovationstreiber in Europa!?« berichteten die Veranstalter und ausgewählte Referenten über Innovationschancen und technologische Weiterentwicklungen, neue Digitalisierungsstrategien und Geschäftsmodelle sowie Wege hin zu einer wertsteigernden Kreislaufwirtschaft im Werkzeugbau und setzten so Impulse für eine langfristig erfolgreiche Ausrichtung der Werkzeugbaubranche.
Neue Chance im nächsten Jahr
Auch im kommenden Jahr werden sich die besten deutschsprachigen Werkzeug- und Formenbaubetriebe wieder untereinander messen. Interessierte können sich schon jetzt unter www.excellence-in-production.de detailliert über den Wettbewerb informieren und ab dem 1. Dezember 2023 registrieren. Alle Teilnehmenden des Wettbewerbs erhalten eine individuelle Auswertung über ihre Stärken und Verbesserungspotenziale.
Nach der Anmeldung füllen alle Teilnehmenden zunächst nur den ersten Teil des Fragebogens mit einer geringen Anzahl zentraler Fragen aus und erhalten auf dieser Basis eine erste Kennzahlenauswertung. In der zweiten Wettbewerbsphase sind detailliertere Fragen zu beantworten und die Teilnehmenden erhalten eine umfangreichere Kennzahlenauswertung. Unter allen Teilnehmenden der zweiten Phase werden außerdem zwei zusätzliche Vor-Ort-Besuche der Aachener Werkzeugbau-Expertinnen und Experten verlost.
Der Wettbewerb wird von der Hasco Hasenclever GmbH & Co. KG als Hauptsponsor, dem KC Kunststoffcluster Österreich und dem Schweizer Werkzeugbau-Verband Swissmem, dem Verband Deutscher Maschinen- und Anlagenbau e.V. sowie der WBA Aachener Werkzeugbau Akademie GmbH unterstützt.
www.excellence-in-production.de