17/11/2021 – Orbital welding
Efficient electrode selection and preparation
Quality pays off: For example, nobody would equip a Formula 1 racing car with inexpensive all-weather tyres. In order to achieve a competitive speed, the vehicle should lie optimally on the track and be perfectly matched to the respective track conditions. Even with TIG arc welding, the tool used for high-quality welds must be adapted to the respective application – and yet many welders use second-class tungsten electrodes that are not matched to the respective process.
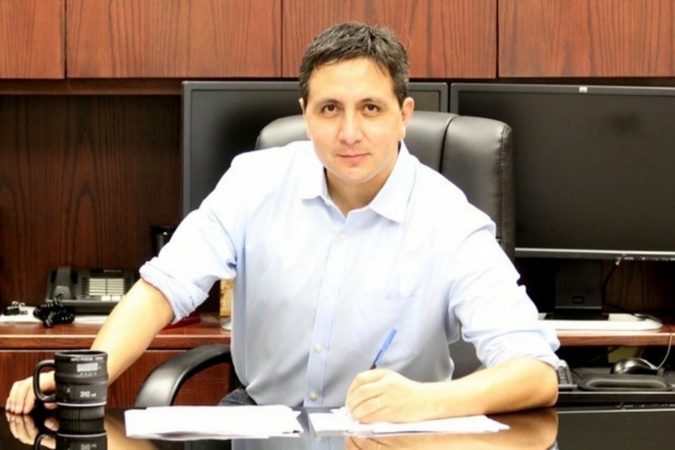
Xavier Jauregui is Vice President of the Technical Department at Arc Machines Inc. © Arc Machines Inc.
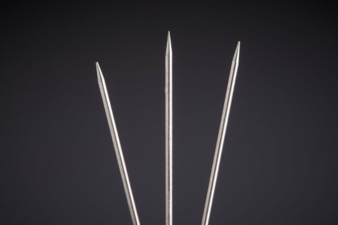
While tungsten electrodes are frequently used in welding, their structure, sharpening and alloy have a previously underestimated influence on consistently good product results in TIG welding. A reproducible weld seam is only possible if the electrode quality and geometry are outstanding. © Society for Wolfram Industrie mbH
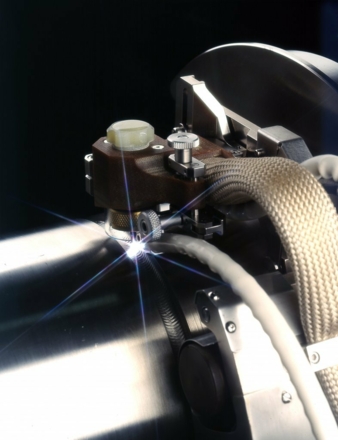
Orbital welding is frequently used in the manufacturing trade, for applications ranging from installing cooling and heating pipes in dairies to welding fuel pipes in the aerospace sector. © Society for Wolfram Industrie mbH
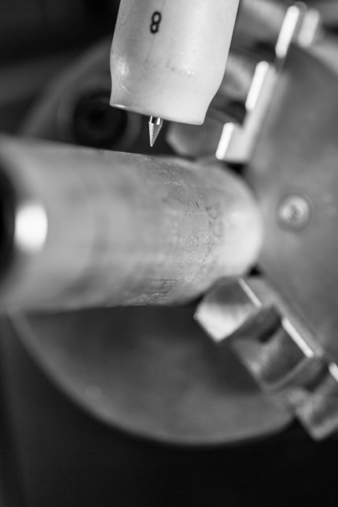
Special emphasis is placed here on the high quality and reproducibility of the weld seams in the interest of occupational health and safety and to avoid possible consequential costs due to deficient processes. © Society for Wolfram Industrie mbH
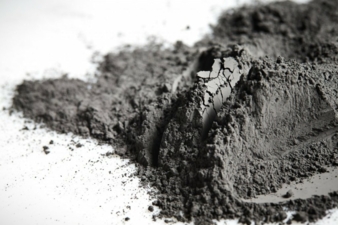
Since the melting points of the materials can differ considerably – tungsten melts at 3,422 degrees Celsius, cerium oxide at 2,400 degrees Celsius - the electrode manufacturers trust the powder metallurgy process. Specific, extremely fine tungsten grain sizes are mixed in order to achieve a homogeneous oxide distribution in the matrix. © Society for Wolfram Industrie mbH