11.12.20 – Dreidimensionale Teileprüfung in Echtzeit
Messen ohne Zeitverlust
Bei den meisten kontaktbasierten Inspektionssystemen sind die Messungen durch lange Zykluszeiten geprägt. Um diese Probleme zu lösen, hat DWFritz Automation die ZeroTouch-Messplattform entwickelt. Das System nimmt die Messungen zügig mittels mehrerer berührungsloser Sensortechnologien dreidimensional und in Echtzeit vor.

DWFritz Automation entwickelte die ZeroTouch-Messplattform, um die Mess- und Prüfzeiten für Teile drastisch zu verbessern. Das System verwendet mehrere berührungslose Sensortechnologien, um die Messungen in drei Dimensionen und in Echtzeit zu erfassen. © DWFritz Automation
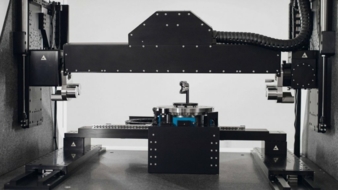
Die Sensorbrücke ist konfigurierbar und ermöglicht eine optimale und geeignete Sensorauswahl für die Teile und Oberflächen zusätzlich zu den zu messenden komplexen Dimensionen. Solche Innovationen im System führen zu einem höheren Teiledurchsatz und einer erhöhten Kapazität, wodurch eine 100-prozentige In-Line-Prüfung statt nur einer Stichprobenprüfung möglich wird. © DWFritz
Konventionelle Messsysteme wie Koordinatenmessgeräte (KMGs) werden üblicherweise für die Qualitätskontrolle in unterschiedlichen Branchen eingesetzt. Bei den meisten herkömmlichen, kontaktbasierten Inspektionssystemen sind die Messungen durch lange Zykluszeiten geprägt. Auch Umrüstungen zur Messung anderer Teile und die damit verbundene Programmierung führen zu Verzögerungen. Außerdem sind kontaktbasierte Messmethoden nicht zur Erzeugung großer Mengen von Datenpunkten geeignet, die bei komplexen Oberflächen erforderlich sind. Aufgrund dieser Einschränkungen sind Systeme wie KMGs keine ideale Lösung für 3D-Inspektionen in der Fertigungslinie.
Um diese Probleme zu lösen, hat DWFritz Automation die ZeroTouch-Messplattform entwickelt. Das System nimmt die Messungen zügig mittels mehrerer berührungsloser Sensortechnologien dreidimensional und in Echtzeit vor. Die proprietäre Software von ZeroTouch erstellt anschließend eine hochpräzise, dichte 3D-Punktwolke. Indem komplizierte Programmiervorgänge vereinfacht werden, verkürzt ZeroTouch zusätzlich die Zeit, die für die Systemkonfiguration benötigt wird, von mehreren Tagen auf wenige Stunden. So können wesentliche Einsparungen bei Produktionszeit und -kosten erzielt werden.
„Die Qualitätskontrolle ist in Produktionsbetrieben von entscheidender Bedeutung“, erklärt David Mendez, Vizepräsident der Geschäftseinheit ZeroTouch bei DWFritz Automation. „Die Vorbereitungen wie die Programmierung sowie der Messvorgang selbst nehmen viel Zeit in Anspruch und verursachen hohe Kosten. Die für die Fertigung erforderlichen Prüftätigkeiten kollidieren mit weiteren Vermessungsaufgaben, etwa mit denen anderer Fertigungslinien, seriennahen Prüfungen oder sogar mit Forschung und Entwicklung.“ Die von DWFritz entwickelte Messplattform verfügt über eine 5-Achsen-Architektur, die Millionen von Datenpunkten pro Sekunde in nur einem Scanvorgang erfasst, um eine dichte 3D-Punktwolke zu erstellen. Das System ermöglicht die schnelle Messung komplexer Teilegeometrien und die präzise Prüfung kompliziertester Teile mit hoher Wiederholgenauigkeit.
Das System verwendet ein planares Luftlagerdesign, das den Toleranzstapelfehler minimiert. Die nahezu reibungsfreie Konstruktion sorgt für eine konstante Hochgeschwindigkeitsbewegung der Präzisionstische und verbessert die Wiederholbarkeit und Reproduzierbarkeit. Taktile Messtaster arbeiten dagegen bei niedrigeren Geschwindigkeiten, da sie physischen Kontakt mit der Werkstückoberfläche erfordern. Kontaktmessungen sind in erster Linie auf 2D-Scans beschränkt, während ZeroTouch komplette 3D-Oberflächen mit einem dichten Gitter von Datenpunkten liefert. Die Erfassung erfolgt mit einer Rate von bis zu 4 Mio. Punkten/s extrem schnell.
Das System kombiniert verschiedene Technologien wie Laser- und chromatische konfokale Sensoren mit hochauflösenden Kameras mit Multispektralbeleuchtung. Des Weiteren ist der Anwender flexibel darin, die richtige Sensortechnologie auszuwählen, um optimale Messergebnisse zu erlangen. Beispielsweise erfordern glänzende oder spiegelnde Oberflächen konfokale oder interferometrische Weißlichtsensoren; matte Oberflächen hingegen Laserprofilsensoren.
Messplattform ist deutlich schneller als herkömmliche Systeme
Bei der Entwicklung von ZeroTouch wurde ein besonderes Augenmerk auf die Probleme gelegt, mit denen konventionelle KMGs konfrontiert werden: schnelle, genaue und reproduzierbare Ergebnisse zu liefern, um mit den Produktionszyklen Schritt zu halten. Die meisten Prüfsysteme haben Schwierigkeiten mit der Geschwindigkeit, einer einfachen Bedienung sowie der Maschinenverfügbarkeit. Folglich eignet sich die traditionelle Messtechnik nicht für Inline-Prüfungen oder Stichproben. Die Bereitstellung eines einfach zu handhabenden Werkzeugs für den Bediener, mit dem er schnelle Qualitätskontrollen verschiedener Arten von Teilen durchführen kann, die von unterschiedlichen Linien hergestellt werden, ist neben der Beschleunigung der Produktionsanlaufzeiten von entscheidender Bedeutung, um die Qualitätssicherung der Fertigungslinien zu gewährleisten. KMGs werden üblicherweise in Prüfräumen mit kontrollierten Umweltbedingungen errichtet, welche oftmals die Maschinenverfügbarkeit beeinflusst. Steht im Fertigungsprozess die Prüfung der Teile im Messraum an, ist oft mit „Warteschlangen“ zu rechnen, da die Maschinenverfügbarkeit begrenzt ist und die Einrichtung der KMGs viel Zeit in Anspruch nimmt.
Die ZeroTouch wurde entwickelt, um genau diese Probleme zu lösen, da sie schnell, flexibel, einfach zu handhaben und mit der Fertigungsumgebung kompatibel ist. Die ZeroTouch ermöglicht außerdem eine 100-prozentige Teileprüfung und zeichnet sich durch eine einfache Bedienung aus. Indem dem Anwender ein einfach zu nutzendes Werkzeug an die Hand gegeben wird, können verschiedene Arten von Teilen, die von verschiedenen Fertigungslinien produziert wurden, schnell geprüft werden. Eine solche Lösung ermöglicht die schnelle Prüfung von Fertigungslinien und beschleunigt die Produktionsabläufe.
Die Architektur von ZeroTouch bietet fünf unabhängige Achsen sowie eine gonio-ähnliche Drehbrücke, die mit mehreren Sensoren – einschließlich Lasern und chromatischer konfokaler Sensoren – ausgestattet ist, sodass keine zusätzliche Zeit für den Austausch eingeplant werden muss. Die Sensorbrücke ist konfigurierbar und ermöglicht eine optimale und geeignete Sensorauswahl, die sich nicht nur für die Messung von komplexen Dimensionen eignet, sondern auch für Teilegeometrien und Oberflächen. Solche Innovationen in Verbindung mit einem horizontalen Drehtisch und drei Translationsachsen führen zu einem höheren Teiledurchsatz und einer erhöhten Kapazität, wodurch eine 100-prozentige Inline-Prüfung anstelle einer reinen Stichprobenprüfung bewerkstelligt wird.
Das innovative Design von ZeroTouch ermöglicht die Wiederholbarkeit in einer von Idealbedingungen abweichenden Fertigungsumgebung. Da die Anlage mehrere Messungen parallel durchführen können, indem sie verschiedene Sensoren verwendet, können Teile und Baugruppen deutlich schneller analysiert werden als ein herkömmliches KMG dazu in der Lage wäre. „Die Sensoren können für die spezifischen GD&T-Messungen und das zu prüfende Teil konfiguriert werden und in einem einzigen Scan kann das System Datenpunkte erfassen, um ein 3D-Modell mit hoher Dichte zu erstellen“, erläutert Mendez. „Dadurch ist es möglich, Objekte aus einer Vielzahl von Materialien mit komplexen Geometrien, einschließlich Bohrungen, Hinterschneidungen, Fasen und Oberflächen, schnell und mikrometergenau zu messen. Gleichzeitig bietet das System eine sehr hohe Reproduzierbarkeit und Wiederholbarkeit der Ergebnisse.“
Die verschiedenen berührungslosen Sensoren auf der Messbrücke lassen sich einfach per Software direkt über die Messplattform kalibrieren. Ein weiterer Vorteil ist die Einfachheit, mit der Teile und Baugruppen auf dem Messtisch platziert werden können, statt komplexe Positioniervorrichtungen zu benötigen. Dies verringert nicht nur die Vorbereitungszeit für die Messtechnik, sondern ermöglicht auch direkte Kosteneinsparungen bei der Konstruktion, Entwicklung und Verwaltung der Vorrichtungen. „Es war außerdem wichtig, dass die ZeroTouch keine Verschleißerscheinungen zeigt und Jahr für Jahr die gleiche Leistung erbringt“, berichtet Mendez. „Deshalb haben wir sie mit einem planaren Luftlagersystem ausgestattet.“ Die beweglichen Teile erzeugen während des Messprozesses praktisch keine Reibung. Teileprüfpläne können innerhalb weniger Stunden erstellt und im Manufacturing Execution System (MES) zur Verwaltung und zum Abruf gespeichert werden. „Der Nutzer wird durch menügeführte, intuitive Werkzeuge unterstützt, sodass tiefe Programmierkenntnisse jetzt überflüssig sind“, erklärt Mendez. „Stattdessen können Prüfpläne mit Hilfe von Drag-and-Drop-Funktionen vorbereitet werden.“
Die Messdaten für jede Komponente werden beibehalten, um die Datenintegrität zu gewährleisten. Danach kann im MES auf komponentenspezifische Pläne zur schnellen Messung zugegriffen werden. Optional lassen sich Komponenten oder Baugruppen mit Barcodes versehen, die von einem Onboard-Barcode-Lesegerät ausgelesen werden können. Der jeweilige Prüfplan wird dann automatisch aus dem MES geladen. Die Steuerungssoftware sorgt für hohe Personensicherheit, denn das System bewegt sich nicht, solange die Türen des Schaltschranks geöffnet sind oder der System-Lichtvorhang gestört wird.
Integrierte Analysewerkzeuge für optimierte Qualitätskontrolle
Die dreidimensionale Punktwolke kann unmittelbar nach dem Messvorgang analysiert werden. Die Integration bewährter Analysewerkzeuge ermöglicht den genauen Vergleich der Scan-Ergebnisse mit CAD-Teilmodellen oder einem zuvor gescannten Referenzteil, um nicht nur geometrische und dimensionale Toleranzen, sondern auch andere unentdeckte Probleme, etwa Fehler im Erscheinungsbild von Oberflächen, zu prüfen. Mit Hilfe der statistischen Prozesskontrolle (SPC) können auch überdurchschnittliche Toleranzabweichungen schnell erkannt und entsprechende Berichte an das MES zurückgeschickt werden. Dies ermöglicht die Anpassung von Prozessparametern in vorgelagerte Fertigungsprozesse, um den Ausschuss im Produktionsprozess zu minimieren.
Das derzeitige System misst 240 x 150 x 190 cm (L x B x H) und wiegt 3550 kg. Es kann Teile mit Abmessungen von bis zu 300 x 300 x 300 mm und einem Gewicht von bis zu 10 kg messen. Es verwendet einen Hochleistungs-GPU-PC mit Intel Core i7-7700T-Prozessor und zwei kapazitive Industriemonitore mit Touchscreen.
DWFritz Automation
Vertretung Europa
Ansprechpartner ist Marc Rosenbaum
3, Rue Emmanuel Philipot, 35240 Saint-Erblon/Frankreich
Tel.: +33 6 77148418
mrosenbaum@dwfritz.com
www.dwfritz.com
Über DWFritz Automation
DWFritz Automation wurde im Jahr 1973 von Dennis Fritz gegründet und hat seinen Hauptsitz in Oregon, USA. Das Unternehmen bot zunächst Ingenieurdienstleistungen an und arbeitete bereits ab den 1980er-Jahren mit weltweit bekannten Marken wie HP und anschließend Intel und Boeing zusammen. In den 1990er-Jahren spezialisierte sich DWFritz Automation zunehmend auf die Entwicklung und Herstellung von hochpräzisen Automatisierungs- und Vermessungslösungen für zahlreiche Branchen wie etwa Luft- und Raumfahrt, Medizintechnik, Maschinenbau, den Automobilbereich sowie Unterhaltungselektronik. Heute beschäftigt das Unternehmen mehr als 500 Mitarbeiter an Standorten in den USA, Frankreich und China.